Managing a fleet of construction vehicles is no easy task, right? Between unexpected breakdowns, skyrocketing maintenance costs, and project delays, it can feel like you’re constantly putting out fires. But what if there was a way to stay one step ahead of these headaches? Imagine cutting down on costly repairs and keeping your equipment running smoothly—without the constant stress. The secret? Construction fleet maintenance software.
This powerful tool can completely transform how you manage your fleet, ensuring your vehicles are always ready for action. In this post, we’ll break down the five must-have features you need in your software to keep your fleet running efficiently and your projects on track. By the end, you’ll see why upgrading your system isn’t just a nice-to-have—it’s a game-changer.
1. Preventive Maintenance Scheduling
Why It Matters:
Let’s face it—no one wants their construction equipment breaking down in the middle of a project. It’s frustrating, expensive, and can throw off your entire timeline. But here’s the good news: with a solid preventive maintenance plan, you can cut down equipment breakdowns by 25%. Imagine the savings on repairs, not to mention the peace of mind knowing your fleet is ready to tackle the next big job.
What’s In It for You?
- Less downtime: Keep your projects moving without annoying delays.
- Longer-lasting equipment: Regular care means your machines stick around longer, saving you big bucks in the long run.
- Safety first: Well-maintained vehicles help you meet safety regulations and avoid fines.
How Can Software Help?
Instead of trying to keep track of all those maintenance schedules in your head or on scattered spreadsheets, fleet maintenance software does it all for you. It sets up automatic reminders for inspections and servicing based on how much you’re using the equipment, its condition, or just regular calendar dates. And the best part? It keeps a log of everything—so you know exactly what’s been done and when. No more missed check-ups or surprise breakdowns.
2. Real-Time Telematics and Monitoring
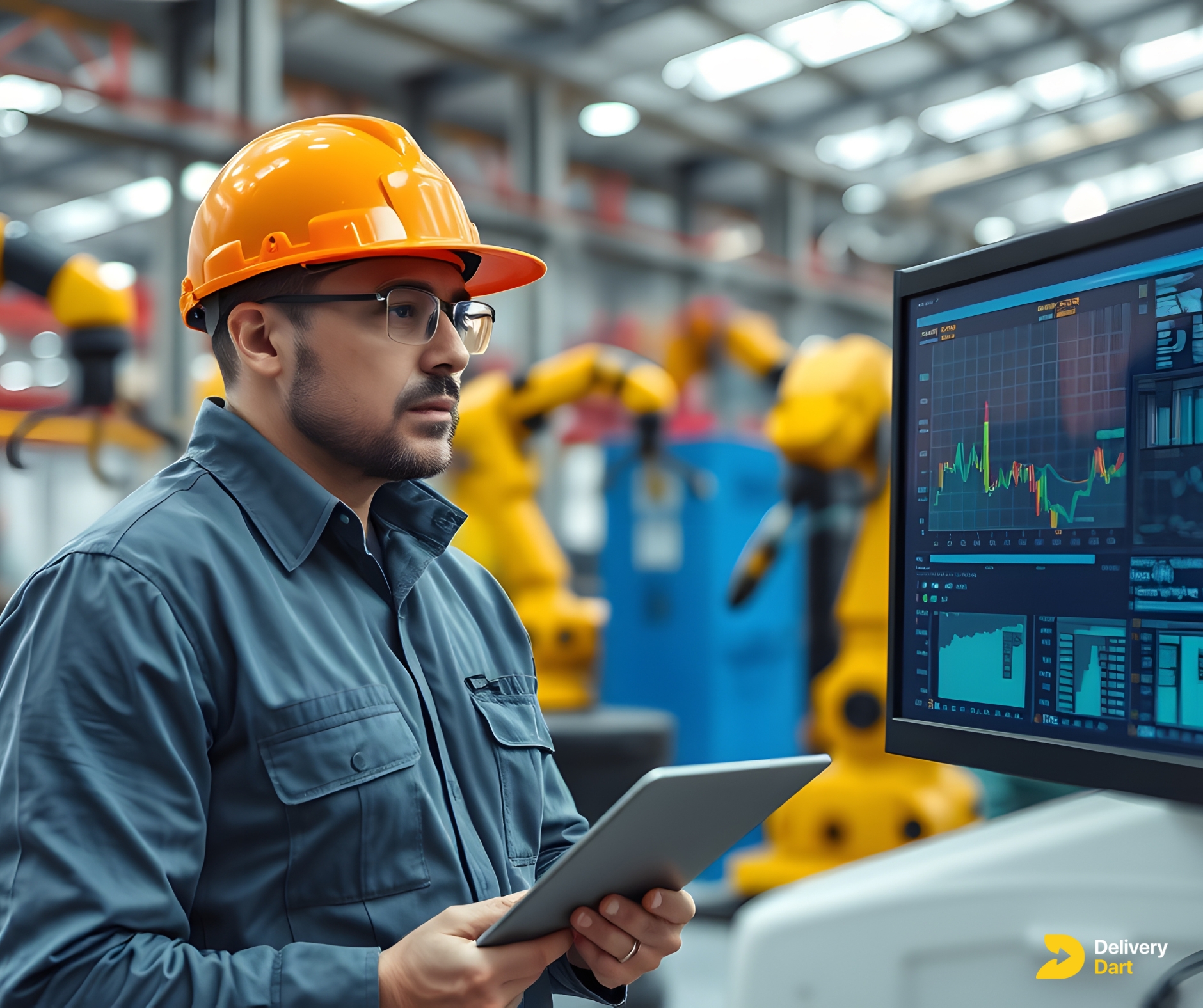
Why It Matters:
Picture this: You know exactly where every piece of equipment in your fleet is, how much fuel it’s using, and whether it’s performing at its best—all in real time. Sounds like magic, right? Well, that’s what telematics can do for you. Companies that use telematics to keep tabs on their fleet have reported 15-30% savings on fuel costs, which means more money staying in your pocket.
What’s In It for You?
- Real-time insights: Know the health and performance of your vehicles the moment something changes.
- Fuel savings: Optimize routes and reduce fuel usage by keeping an eye on driver habits and vehicle efficiency.
- Prevent bigger issues: Spot small problems before they turn into costly repairs, keeping your fleet running smoothly.
How Can Software Help?
Fleet maintenance software that’s integrated with telematics is like having an all-seeing eye on your operations. You’ll get instant alerts about mechanical problems, track your vehicles with GPS, and even set up virtual boundaries (geofencing) to keep everything where it should be. By having this level of control, you can fix issues before they snowball into major headaches.
3. Comprehensive Work Order Management
Why It Matters:
Trying to juggle repair requests, part replacements, and inventory for a whole fleet? It can feel like a full-time job just keeping everything straight! But with a work order management system in place, you don’t have to worry about anything slipping through the cracks. This feature keeps all maintenance tasks neatly organized, so nothing gets missed. And the best part? Everything’s documented and tracked, meaning smoother operations and way fewer surprises.
What’s In It for You?
- Easier task assignments: No more confusion over who’s doing what—mechanics and technicians get clear, automated assignments.
- Real-time inventory tracking: Know exactly what parts you have on hand and when you’ll need more, so you’re never caught off guard.
- Maintenance transparency: Keep a clear audit trail of every repair and part replacement, so you’re always on top of what’s been done and what still needs attention.
How Can Software Help?
Fleet maintenance software takes the hassle out of managing work orders. It automatically creates and updates repair tickets, and keeps managers in the loop on every repair’s progress. No more missed tasks or last-minute scrambling—just smooth, organized operations that keep your fleet running like a well-oiled machine.
4. Asset Tracking and Lifecycle Management
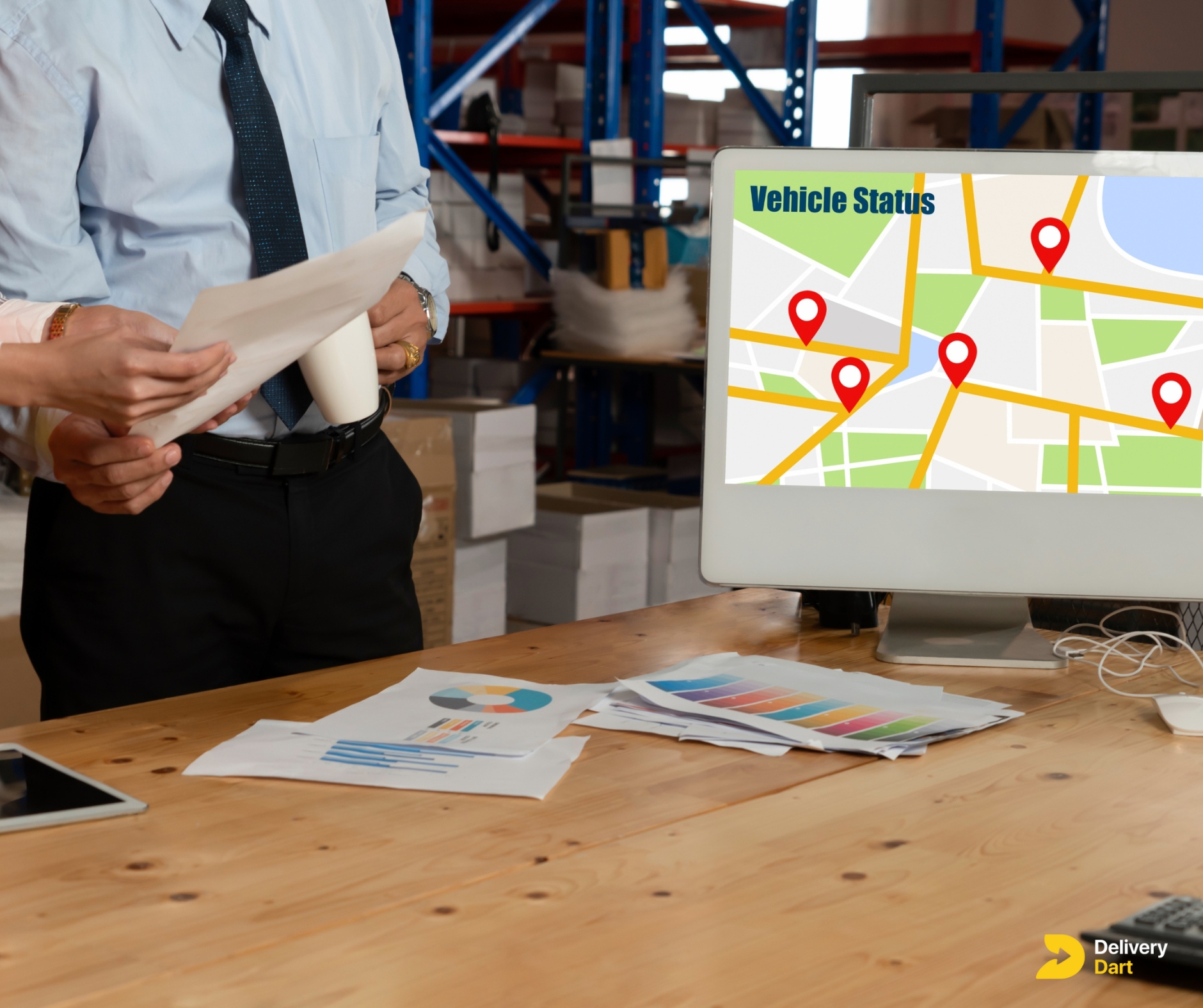
Why It Matters:
Keeping track of your construction fleet’s assets—from pickup trucks to heavy-duty bulldozers—can be a serious challenge. With so many moving parts (literally!), it’s easy to lose sight of where equipment is, how much life it has left, and when it might need major repairs or replacement. This is where asset tracking comes in, helping you manage the lifecycle of each vehicle or machine, so you’re never blindsided by unexpected breakdowns or surprise costs.
What’s In It for You?
- Longer equipment lifespan: By closely monitoring usage, you can keep your high-value machines running for longer.
- Smarter spending: Avoid unnecessary purchases and plan for replacements well in advance—no more last-minute scramble for new equipment.
- Data-driven decisions: Get real insights into your fleet’s performance and health, helping you make better choices about when to repair, upgrade, or retire assets.
How Can Software Help?
Fleet maintenance software does all the heavy lifting here (pun intended!). It gives you clear data on how your equipment is being used, making it easier to predict when you’ll need repairs or replacements. With this insight, you can plan ahead, budget more effectively, and keep your fleet running smoothly without any nasty surprises down the road.
5. Reporting and Analytics
Why It Matters:
In today’s world, data is everything—and that’s especially true when managing a construction fleet. The more you know about your fleet’s performance, the better decisions you can make. With the right reporting and analytics tools, you can keep an eye on important metrics like fuel usage, maintenance costs, and downtime. In fact, companies using data analytics effectively have seen maintenance costs drop by 10-15%, which means major savings for your bottom line.
What’s In It for You?
- Spot performance trends: Identify patterns in your fleet’s performance so you can tackle issues before they get expensive.
- Optimize maintenance schedules: Use real-world data to fine-tune when and how often your equipment needs attention.
- Boost productivity: Eliminate inefficiencies by knowing exactly where your fleet can improve, keeping your operations running smoothly.
How Can Software Help?
Fleet maintenance software takes all that complex data and turns it into easy-to-read reports. Whether you want to track fuel consumption, compare maintenance costs across vehicles, or get insights into downtime, these tools give you the numbers you need to make smarter decisions. In short, you’ll have a crystal-clear view of your fleet’s health and performance, letting you run a tighter, more efficient operation.
Ready to Level Up Your Fleet Management?
With the right construction fleet maintenance software, you’re not just maintaining your vehicles—you’re supercharging your entire operation. From preventive maintenance that keeps downtime at bay to real-time telematics that gives you instant insights, these features work together to make your fleet more efficient, productive, and cost-effective. Imagine being able to streamline work orders, track every asset’s lifecycle, and use data-driven reports to stay ahead of the game—now that’s a fleet manager’s dream!
And if you’re already thinking of boosting efficiency beyond just your construction fleet, tools like DeliveryDart make it easy to manage deliveries and keep your business moving forward. So why wait? It’s time to embrace the future of fleet management and watch your operations soar to new heights!